Topic last reviewed: June 2023
Sectors: Downstream, Midstream, Upstream
Introduction
A heat pump is a device that uses mechanical energy to transfer thermal energy for either heating or cooling. Heat pumps consist of a compressor, condenser, expansion valve, and evaporator. A simplified schematic of a heat pump is illustrated in Figure 1. Heat pumps can be a bidirectional thermal transfer device, reversing the role of the evaporator and condenser. Commercial heat pumps have become very common in building heating and cooling.
Industrial heat pump applications are not common due to historic availability of other heating and cooling sources. As companies become more focused on reducing CO2 emissions, industrial heat pumps may introduce energy efficiency and environmentally friendly heating and cooling. One example may be to use low-grade waste heat (like a product rundown) to produce a more useful, higher temperature fluid, such as steam.
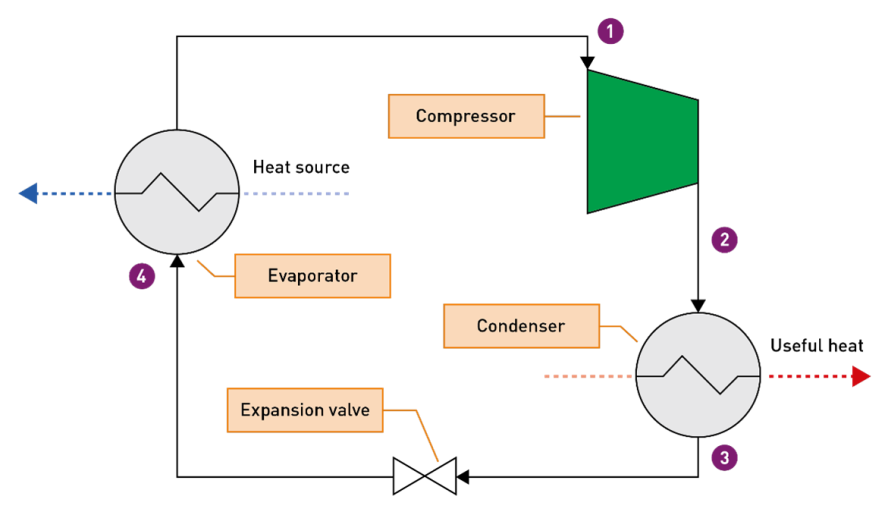
The associated temperature-entropy diagram for the system is illustrated in Figure 2.
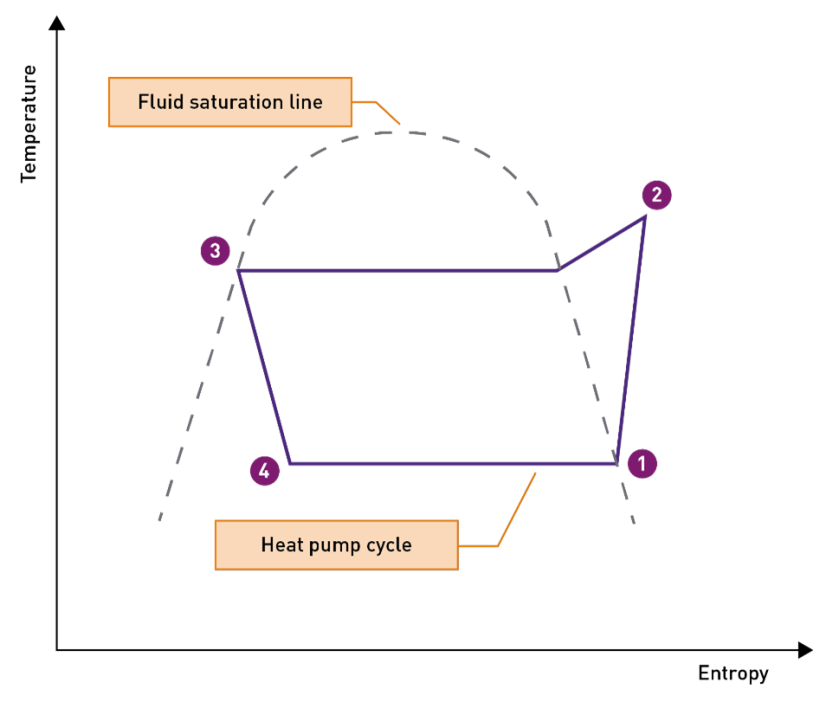
Application
Almost all heat pumps are based on a mechanical vapour compression (MVR) system or on a physical, chemical absorption cycle. Vapour compression heat pumps can be driven by electricity, an internal combustion engine, or may use process fluid itself as the working fluid in an open cycle (such as mechanical vapour recompressors). A common mechanical vapour recompression application in oil refineries is a propane/propylene (C3/C3=) splitter where energy is added to the overhead vapour by compressing it. This heats the vapour, which is then used as heat for the column reboiler instead of steam. MVR works well as there is little temperature difference between the overhead and the reboiler. MVR begins to lose some of its benefit as the temperature increases. This is why MVR is not currently seen in other refinery applications. Absorption heat pumps are thermally driven, which means that heat, rather than mechanical energy, is supplied to drive the cycle.
Traditionally, the most common working fluids have been chlorofluorocarbons (CFCs). Given their high ozone-depleting potential, other adverse environmental impacts, and regulatory phase out, these are now being replaced by more suitable natural working fluids, such as ammonia, propane, water, carbon dioxide, and air. Proprietary blends of environmentally friendly refrigerants are also being developed, which may have applications as working fluids in industrial heat pumps.
Electric heat pumps for heating buildings typically supply 100 kWh of heat with just 20–40 kWh of electricity. Many industrial heat pumps use a waste heat stream so they can supply the same amount of heat with even less electricity. Ground-source heat pumps use the ground, which maintains a relatively constant temperature of 6–20°C at three metres or more below the surface, either as a heat source or as a sink, depending on the season.
For a more detailed description of this technology, please refer to:
- Office of Energy Efficiency & Renewable Energy (U.S Department of Energy)
- Industrial Heat Pumps for Steam and Fuel Savings: A Best Practices Steam Technical Brief (U.S Department of Energy)
- Waste Heat Recovery: Technology & Opportunities in US Industry (U.S. Department of Energy)
- Heat Pumps – Analysis (IEA)
- Heat Pumping Technologies (Technology Collaboration Programme by IEA)
- Industrial heat pumps, Second phase (Heat Pumping Technologies)
- Final Report Annex 48: Industrial Heat Pumps, Second Phase (Heat Pumping Technologies)
- European Heat Pump Association
- Geothermal Exchange Organization
Technology maturity
Commercially available | Yes |
---|---|
Offshore viability | No (currently being explored with the ocean as a geothermal heat sink, but has not yet been implemented). |
Brownfield retrofit | Yes |
Years experience in the industry | 20+ |
Key metrics
Range of application | Very common in building heating/cooling at many different sizes. Common in distillation columns if top/bottom temperatures are close together. |
---|---|
Guideline capital costs | Costs are relatively cheap for building applications. No data available for oil and gas industry installations, though it is cheaper to install new than retrofit later. |
Guideline operational costs | Less fuel and energy used than traditional heating and cooling systems, saving operational costs. |
Typical work description | In building applications, heat pumps are more likely to be used in regions where both heating and cooling are required, depending on the season (such that the heat pump can replace both boiler and air conditioner). |
Decision drivers
Technical |
|
---|---|
Operational |
|
Additional comments
Efficiency performance of heat pumps is referenced as coefficient of performance (COP) or primary energy ratio (PER). COP is defined as the ratio of thermal energy delivered by the heat pump, to the mechanical energy supplied to operate the compressor. PER is defined as the ratio of useful energy delivered by the heat pump, to the primary energy input. Primary energy can be measured as renewable or non-renewable energy. Typical COP ranges for electric building heat pumps are two to five. In industry they be as much as eight times higher. The PER for a heat pump can typically be between one to two. As industrial heat pump technology continues to advance, it is recommended to consult heat pump manufacturers for current COP and PER values, based on specific industrial application.
Heat pump efficiency decreases as the desired temperature lift increases. This is one reason why heat pumps are less common in distillation columns with condensers and reboilers at very different temperatures.
Alternative technologies
The following items provide some similar benefits to heat pumps, though they also have some different characteristics:
- Gas (or biogas)-fired burners/steam generators/boilers, though they may not be as energy efficient
- Solar-powered absorption chillers or heating systems, though this involves first making electricity and then using it to chill or heat
- Combined heat and power (CHP), though it may not be as energy efficient.
- Heat exchangers (between high enthalpy fluids needing cooling and other streams needing heating), though this cannot increase the temperature of a stream without first having a hotter stream to transfer heat from
Operational issues/risks
- Heat fluctuation (if using waste heat)
- Integration with existing industrial systems
- Water (if using open loop ground heat)
- System complexity, potential maintenance issues
- In the case of ground source heat pumps, drilling and completion could be expensive
Opportunities/business case
- Heat pump with higher output temperature (such as 150°C or above) for industrial uses (while maintaining reasonable efficiency): not common now
- When a heat pump is being considered, it is important that the entire system is studied and not just a single piece of equipment
Industry case studies
Distillation column heat pump application
Leonardo Energy, Application note: industrial heat pumps [Reference 1]
A case study was prepared to address the high energy costs of operating a steam-heated reboiler on a distillation column using heat pump technology. The simplest alternative to conventional column design is to replace the steam heating in the reboiler with a condensing refrigerant, at a relatively high pressure, and replace the condenser coolant with an evaporating refrigerant at low pressure. The reboiler then becomes the condenser and the column condenser becomes the evaporator in a heat pump system. The column design is unchanged, but the heat exchanger design is different from a conventional distillation column operational standpoint. Figure 3 illustrates the heat pump concept for the distillation column application.
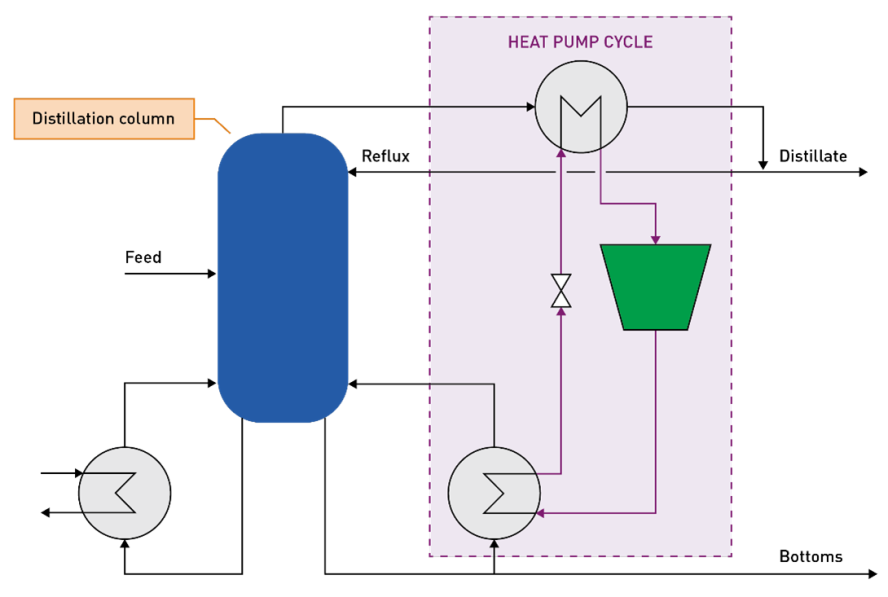
Figure 3: Distillation unit with closed loop heat pumping cycle
Baseline scenario: the base design for efficiency comparison is a conventional distillation column with steam heated reboiler, using natural gas to generate steam.
Energy efficiency project activity: use a condensing refrigerant in the reboiler to replace steam heat, and the evaporating refrigerant in the column condenser to replace the cooling medium. The refrigerant cycle then effectively acts as a heat pump to provide both heat and cooling.
Performance specifications:
- Column top pressure/temperature: 175 mbar/124°C
- Column bottom pressure/temperature: 199 mbar/135.5°C
- Boil-up rate: 36,000 kg/hr
- Heat of vaporization (top): 74.5 kcal/kg
- Energy required for boil-up: 3,120 kW
References:
1. Bohdan S. ‘Application note: industrial heat pumps.’ In Leonardo Energy. January 2015.